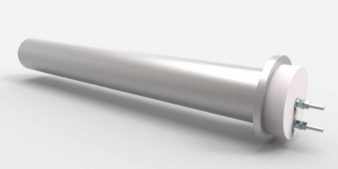
In the industrial world, the choice of heating method for your furnace can significantly impact both the efficiency of your operations and the quality of your products. With various technologies available, each with its unique advantages and applications, selecting the right industrial furnace heating method becomes crucial for businesses aiming to optimize their processes and reduce costs. This blog explores the main types of industrial furnace heating methods, their applications, and how to determine which is the most suitable for your business needs.
Understanding the Different Heating Methods
1. Electric Heating
Electric furnaces use electric elements to heat the interior space and the material inside. This method is known for its high efficiency, as it can convert almost all the consumed electrical energy into heat. Electric heating offers precise temperature control, making it ideal for processes requiring tight temperature tolerances.
Pros:
High energy efficiency
Precise temperature control
Environmentally friendly with lower emissions
Cons:
Higher electricity costs in areas with expensive power rates
Limited in scale due to electrical supply constraints
2. Gas Heating
Gas furnaces heat the chamber by burning natural gas or other fuel gases. They are widely used in industrial furnace heating for their capability to reach high temperatures and their cost-effectiveness in regions where gas is cheap and readily available.
Pros:
Cost-effective in regions with low gas prices
Capable of reaching very high temperatures
Suitable for large-scale operations
Cons:
Emissions need to be managed
Requires a steady supply of gas, which can be a constraint in some areas
3. Induction Heating
Induction heating works by inducing an electric current into the material to be heated, causing it to warm up due to its own electrical resistance. This method is highly efficient and precise, offering uniform heating and control.
Pros:
Extremely efficient and precise
No direct contact, reducing contamination risk
Quick heating rates
Cons:
High initial equipment cost
Limited to materials that are electrically conductive
4. Oil Heating
Oil-fired furnaces use oil as the fuel to generate heat. While less common than gas and electric furnaces, they are used in specific industries where oil is a preferred energy source due to availability or cost.
Pros:
Good for areas where oil is cheaper than gas and electricity
High heat output
Cons:
Higher emissions compared to electric heating
Requires storage for oil, increasing the potential for spills and environmental hazards
Selecting the Right Heating Method for Your Business
Choosing the best heating method for your industrial furnace involves considering several factors specific to your operation. Here are key considerations to guide your decision:
1. Operational Cost
The financial implications of operating your furnace can have a profound impact on your overall profitability. Conduct a thorough assessment of the expenses associated with running different heating methods, encompassing electricity, gas, or oil costs prevalent in your geographical area. Delve deeper into the comparative efficiencies of each heating method, recognizing that while electric furnaces might boast higher efficiency rates, the prevailing cost dynamics might render gas or oil alternatives more economically viable.
2. Temperature Requirements
The diverse array of industrial processes necessitates a keen understanding of the temperature ranges imperative for optimal functionality. Tailor your heating method selection to align with the specific temperature exigencies of your operations. For applications demanding elevated temperatures, gas furnaces could emerge as the preferred choice, whereas processes mandating meticulous temperature control might find electric furnaces to be more amenable.
3. Environmental Considerations
In an era increasingly cognizant of ecological imperatives, the environmental ramifications of your heating method selection warrant meticulous scrutiny. Prioritize the mitigation of your carbon footprint by exploring cleaner alternatives such as electric heating, particularly if sourced from renewable energy reservoirs. However, acknowledge the nuanced interplay of regional energy production methodologies and regulatory frameworks in influencing the overall environmental impact of each heating method.
4. Scalability
Anticipate the scalability prerequisites inherent in your operations when deliberating upon the optimal heating method. Electric and induction furnaces present themselves as highly adaptable solutions, offering unparalleled flexibility in temperature modulation to cater to the exigencies of both small-scale enterprises and precision-oriented industries. Conversely, gas and oil furnaces epitomize scalability in the context of large-scale industrial applications, adeptly accommodating the imperatives of high heat generation and voluminous throughput.
5. Material Considerations
The intrinsic properties of the materials under processing exert a pivotal influence on the suitability of the chosen heating method. While induction heating stands out as an exemplary choice for metals owing to its unparalleled precision and efficiency, its applicability to non-conductive materials might be limited, necessitating a judicious assessment of material-specific considerations in your decision-making paradigm.
Conclusion
The choice of an industrial furnace heating method is a critical decision that can affect your operation's efficiency, cost, and environmental impact. By understanding the pros and cons of each method and carefully considering your specific needs, you can make an informed decision that aligns with your business goals. Whether it's the precision of electric heating, the scalability of gas heating, the efficiency of induction heating, or the cost-effectiveness of oil heating, the right choice depends on a balance of operational, environmental, and financial factors specific to your industry and processes.
Write a comment ...